Producción
Los ciclos de producción y las pruebas internas se realizan mediante las líneas más modernas SMT (Surface Mounting Technology) y PTH (Pin Through Hole), con la asistencia de máquinas pick&place, soldadoras de onda, hornos de refusión, sistemas de inspección óptica (AOI), robots de ensamblaje. La capacidad de nuestros establecimientos es de miles de componentes/hora, lo que permite conjugar una velocidad elevada, la precisión y un time-to-market sumamente reducido. El proceso productivo es plenamente conforme con las directivas ambientales y de compatibilidad ecológica RAEE, ROHS e REACH. Al final de la línea se somete a todos los productos a unos severos test de prueba automática con generación de informes de prueba. Gracias a los almacenes verticales automatizados de una altura de 12 metros y una capacidad de 1.000 m2 hay siempre disponibles como media 80.000 piezas listas para la entrega. La integración con el sistema ERP garantiza la completa trazabilidad de los productos. .
PROYECCIÓN
- SENECA ha efectuado inversiones importantes en sus laboratorios a fin de poder efectuar test de verificación a todos los niveles del proceso productivo.
- Tecnologías programables FPGA, PsOC, CPLD
- Las tecnologías de transmisión y programación más avanzadas: ASIC, DSP, MEMS, LVDS, VHDL…
- Software avanzados de proyección: Electronic PCB CAD(PROTEL DXP), Protyping (LPKF PROTOMAT 60), Electric CAD / Mechanic (AUTOCAD), 3D Modeling (CADMATIC)
|
|
PRODUCCIÓN
- Líneas Pick&Place de última generación SMT (Surface Mounting Technology)
- Montaje robótico
- Sistemas AOI (Automated optical inspection)
- Sistemas ATE (Automatic Test Equipment)
- Conformidad medioambiental RAEE, ROHS y REACH
- Test burn-in efectuado en todo el proceso productivo
- Alto nivel de inmunidad intrínseca a las interferencias electromagnéticas.
- Productividad flexible un millar de piezas cada hora.
- Hornos de refusión
- Soldadura de onda
- Laboratorio interno para los test EMC
- Trazabilidad global
- Cambio de producción rápido
|
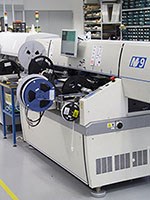
|
ALMACÉN
- Sistema de elevación vertical construido para memorizar los objetos de almacenamiento voluminosos.
- Más de 12 metros de altura.
- Gran capacidad de almacenamiento (1.000 m2 de almacén)
- Extracción bandeja automática o manual mediante carro elevador.
- Rápida integración de escáner de códigos de barras para la identificación del orden, recogida y confirmación.
- Conexión en tiempo real con los sistemas ERP, que asisten al operador y le permiten trabajar con la máxima precisión.
- Trazabilidad total de los lotes
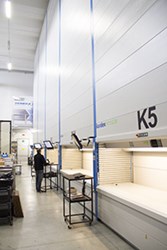
|